Understanding Predictive Maintenance Software: What It Is and How It Works
The way that many industries conduct equipment maintenance is evolving due to predictive maintenance software. Instead of relying on set schedules or waiting for breakdowns, predictive maintenance software predicts defects and solves problems before they happen. This is through the real-time data analysis of the machines by combining the past and present to observe and raise warnings on potential mishaps early enough.
It starts with sensors on the equipment collecting data like temperature, vibration levels, and noise. It studies the data collected and searches for patterns that could signal impending trouble. For instance, if some machine starts vibrating more than the usual rate, it might indicate that one part should soon be attended to before it wears out.
Predictive maintenance software’s true strength is in its capacity to deliver lucid, useful information. This lets the maintenance teams prepare for actual repairs during scheduled downtime instead of during sudden breakdowns; this minimizes interruptions and also prolongs running time before the equipment finally breaks down, hence saving money in the long haul.
Important Qualities of Predictive Maintenance Tools
In choosing software for predictive maintenance, determine the features that would make it perform as you want and be easy to use:
- Integration with current systems and data sources: The program should work well with the systems and data sources you now use. It should support multiple sensors and formats to give an all-round view of your equipment’s health.
- Real-Time Monitoring: Continuous monitoring of the equipment is vital so that the potential failure can be found in time. The software should present data in real-time, so the maintenance teams can respond to their requirements without delay.
- Integration with current systems and data sources: The program should work well with the systems and data sources you now use. Advanced algorithms should be used for the analysis of historical data so that the prediction of future failures will be precise about the equipment.
- User-Friendly Interface: There should be a very simple and intuitive interface that allows users to find data, generate reports, and set alerts without extensive training.
- Reporting and Analytics: There should be detailed reporting tools as well as dashboards available. This feature enables teams to track trends and gain some insight into their operations to make more informed decisions with more customizable visuals and reports.
Top Industries Benefiting from Predictive Maintenance Solutions
Predictive maintenance software is versatile and can be applied in so many industries; each has some tremendous benefits:
- Manufacturing: In manufacturing, equipment downtime results in huge losses in production. Predictive maintenance identifies problems early enough, keeps machines running with minimal maintenance costs, and no instances of delay in production.
- Energy: Power plants and energy facilities use predictive maintenance to keep their critical equipment, like turbines, generators, and transformers, running in perfect order. Such equipment failure can provoke an expensive outage or have a steady supply of energy disrupted.
- Transportation: From air power to rail and shipping, Predictive maintenance keeps vehicles and equipment reliable; which improves safety, minimizes unexpected breakdowns, and runs services to schedule.
- Health Care: Predictive maintenance is essential in keeping medical devices such as MRI machines and ventilators in good working condition. This ensures such equipment is always ready to provide undisturbed care for patients.
- Oil and Gas: Damage to equipment in the oil and gas industry can lead to environmental disasters as well as a waste of financial assets. Predictive maintenance prevents large-scale problems from occurring as pipeline and pump problems as well as drilling equipment can be detected before failure.
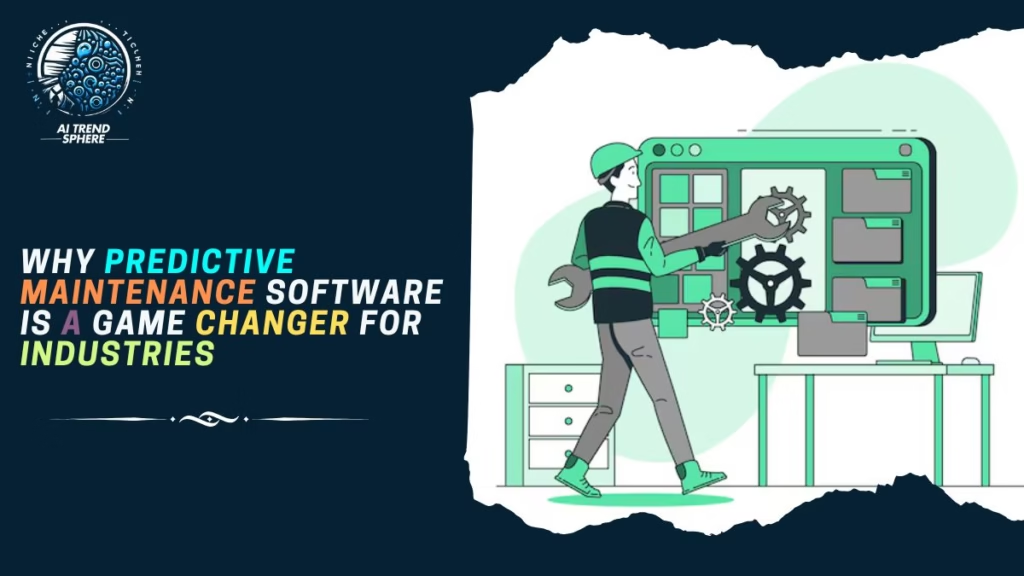
Challenges in Implementing Predictive Maintenance Software and How to Overcome Them
Predictive maintenance comes with numerous advantages; however, setting up the predictive maintenance software system can pose the following obstacles in many ways:
- High Initial Costs: This needs huge initial spending in terms of technology and infrastructure to set up the predictive maintenance software. However, long-term savings through fewer breakdowns and longer equipment life usually pay for the initial costs. A cost-benefit analysis can make a good case for investment.
- Data Management: Huge amounts of data coming from a variety of sources can be quite overwhelming. This is something that can be dealt with through proper usage of strong data integration tools, storage systems that work, and having the right people who know what to do with the data to handle it effectively.
- Technical Expertise: Predictive maintenance functions with advanced technology that require specific skill sets. Training your employees and recruiting competent individuals will facilitate this. Another excellent proposal for filling in this knowledge gap is to look for partnering with software service providers for continued support.
- Resistance to Change: The negative impact: People working with legacy maintenance practices do not like new practices. To counter this challenge, engage the employees early in the process and show them the benefits predictive maintenance can bring; then train them well so that they are confident with the new system.
- System Integration: Connecting the predictive maintenance software to existing systems can be cumbersome. Therefore, ensure that you choose a software system that can easily be connected with your current setup and offers several integration options using APIs, among other options. Collaboration with experienced vendors who understand the requirements of your industry will also help.
Predictive Maintenance’s Future: Innovations and Trends to Keep an Eye on
Predictive maintenance has a bright future ahead of it, driven by emergent changes and novel approaches. The key trends and improvements in the lines include:
- Artificial Intelligence and Machine Learning: AI and machine learning are getting quite advanced, so the systems would make it possible for predictive maintenance systems to predict much more accurately. These technologies mean that systems are self-learning, which progressively enhances the depth of their analysis with time.
- IoT Integration: One of the critical elements of IoT is connecting more and more devices and sensors, thus building an actual network of real-time data, which supplies much richer views of equipment performance and predictive maintenance on entire systems rather than individual machines.
- Edge Computing: Rather than relying strictly on cloud-based systems, edge computing processes data locally, near the source. That can accelerate analysis time and reaction time, such as in a remote or mission-critical device.
- Digital Twins: An electronic replica of a real asset is called a digital twin. This is truly a game-changer because it enables predictive maintenance systems to simulate equipment behavior and test scenarios before they ever occur in the real world.
- Better User Interfaces and Insights: Tools for Predictive Maintenance Solution. Predictive maintenance tools are now getting more user-friendly dashboards and analytics. These tools give clearer insights to make it easier for teams to act quickly and effectively.
- Sustainability Focus: The sustainability focus of industries hits the mark with predictive maintenance because it aligns with this goal. The reduction of equipment failure and waste, which further promotes more efficient resource usage, reduces carbon footprint.
Conclusion
The way that industries handle equipment maintenance is being completely transformed by predictive maintenance software. It can pick potential problems early and provide for the prevention of any potential downtime with maximum efficiency. Highly advanced key features such as data integration, real-time monitoring, and advanced algorithms make the solutions very effective.
The rest of which have to do with initial cost and large volumes of data requiring special skills will be provided for with some smart planning and investment.
Brighter Future of Predictive Maintenance: AI, IoT, cloud solutions, edge computing, and predictive analytics boost precision, hasten, and make it accessible. These innovations bring reliability and low costs, making industries keep themselves ahead in the row.
Predictive maintenance software reduces the downtime of industries, extends the life of equipment, and streamlines the entire operations; it is far from a “technical” move towards a more efficient and reliable future.
To Read About How Art Prompts and AI Spark Creative Growth.